Right experience!
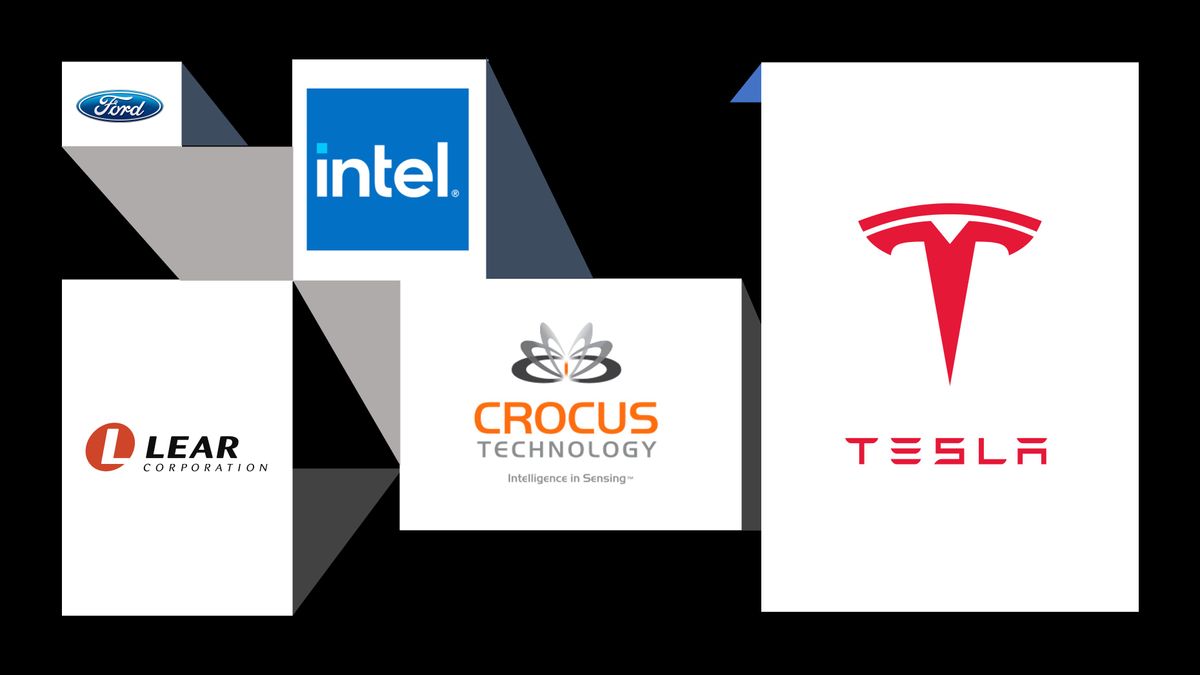
This is a quick summary of my experience, for more details check my Bio.
Program Manager Technical, Automotive and Quality Systems
Intel Programmable Solutions Group, Intel Corp.
July 2015 – Ongoing San Jose, CA, USA
Responsible for defining and implementing QMS processes and standards to drive toward zero-defects and continuous improvement.
Accomplishments:
- Co-defined and built the Quality Management System (QMS) for Intel’s Field Programmable Gate Array (FPGA) business to achieve ISO 9001:2015 Certification, and satisfy customer requirements.
- Integrated Advanced Product Quality Planning to Quality Release Criteria into Product Lifecycle Design and Development Process for FPGAs.
- Improved Risk Management by implementing Failure Mode and Effect Analysis (FMEAs), for FPGAs Design and Development process.
- Standardized the International Material Data System activities across the globe to improve from 20 percent to 99 percent first-time-through customer acceptance.
- Go-to engineer for Quality Systems improvements, such as ISO 9001 and IATF 16949, supporting other Intel business units across the globe.
Program Manager Technical, Operations & Quality Management Systems
Crocus Technology.
August 2018 – August 2023 San Jose, CA, USA
Accomplishments:
- Co-defined and implemented the operational framework and Quality Management System (QMS) for Crocus Magnetic Sensors Business.
- Achieved ISO 9001:2015 Certification meeting customers requirements.
Product Excellence Engineer Tesla Inc.
April 2014 – July 2015 Fremont, CA, USA
Responsible for product quality of high and low-voltage distribution systems for Tesla Model S and X vehicles. In charge of supplier development, with accountability for three VPs of Operations and three VPs of Quality (from the supplier base) for improvements and cost reduction.
Accomplishments:
- Increased assembly plant capacity by 25 percent by implementing initiative to outsource 90 percent of high-voltage cable manufacturing.
- Closed deal with Tier 1 supplier, Yazaki, to open two dedicated manufacturing sites to support Tesla.
- Certified manufacturing processes and controls for outsourced business to Yazaki.
- Reduced cost of 12V battery cables by 90 percent resulting in $32M annual savings for the HV battery pack by improving Bizlink manufacturing processes in Shenzhen, China.
Supplier Technical Assistance Engineer (STA) Ford Motor Company.
Jan 2011 – April 2014 Mexico City, MX
Corporate supplier developer for electrical commodity components, supporting all Americas vehicle assembly sites for Ford and Lincoln platforms. Active member of the Global Sourcing Council.
Accomplishments:
- Managed 10+ supplier sites from different GEOs, holding accountable VPs of Quality for improvements, achieving:
- PPM reduction by 23 percent better than objective
- Zero Tier 1 manufacturing “stop ships”
- Zero capacity shortages
- Three business transfers with zero vehicle assembly interruptions
- Developed and implemented innovative, new manufacturing processes for High Voltage Cables; now adopted by Tesla, Fisker Karma and multiple leading EV car manufacturers.
- Go-to engineer for supplier quality and development, related to High Voltage Electrical Distribution System technologies, for Hybrid Electric Vehicles (PHEV, FHEV) & Battery Electric Vehicles (BEV).
Supplier Quality Assurance Engineer Lear Corporation.
Jan 2009 – Jan 2011 Cd. Juarez, Chihuahua, MX
Responsible for bill of materials (BoM) for the manufacturing of seats and headrests.
Accomplishments:
- Ensured product quality for over 3k parts, corresponding to 37 suppliers assigned in yearly basis, for seats and headrest assembly, for GM, Ford, BMW, Hyundai, Toyota and BRP Customers.